CNC Router Online Help and Troubleshooting Guide
Machine Doesn't Move
Controller Not Enabled
Scenario:You are repeatedly getting one of the following two message boxes:
or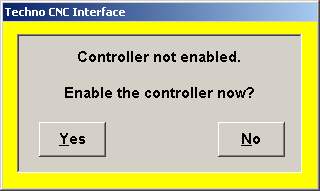
Problem: The Emergency stop loop has been tripped or the machine is not connected.
Solution: Ensure the Emergency Stop Switches are disengaged by pressing them in and then rotating them out. Then try to enable the controller again.
If the problem persists: If your control box has a ready light, while watching the ready light, click to enable the controller. The exact moment you click to enable, the ready light may blink. You may need an assistant to click to enable while you watch the ready light.
Note that your control LED badge may be blue and labeled with different text. The ready light is the only important LED for this test.
If the ready light blinks one time like this (this video cycles every 10 seconds, be patient):
|
The problem is the E-stop loop. Note that the E-stop loop runs through not only the emergency stop switch, but all of the motors as well. This is done to prevent a dangerous situation.
- Follow this link if the Ready light DOES blink when you attempt to enable. Estop_loop_broken
- Follow this link if the Ready link DOES NOT blink when you attempt to enable. Estop_noblink
- Follow this link if you DO NOT have a Ready light on your control box. Estop_no_ready_light
|
Estop loop broken
Scenario: The ready light is blinking on the controller when the user attempts to enable, but the emergency stop is not the cause. The following screen persists:
|
or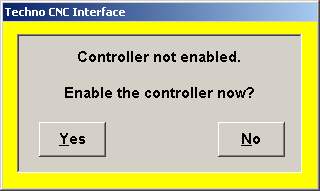 Problem:
The Emergency stop loop has been tripped.
The emergency stop loop is run through all of the motors as well as the E-stop button.
It must be determined which segment of the E-stop loop is broken.
Solution: Before doing any work on the machines, switch off and lock out power to the control box.
›Check all cables going into motors. Ensure they are completely engaged and screwed in tightly.
›Check all cables going into the control board inside the control box. Ensure they are completely engaged and screwed in tightly.
If the problem persists, you will next need to isolate the problem. Find the jumper block on the control board. (Determine your Controller box)
|
LC Plus Control Board E Stop Jumper header 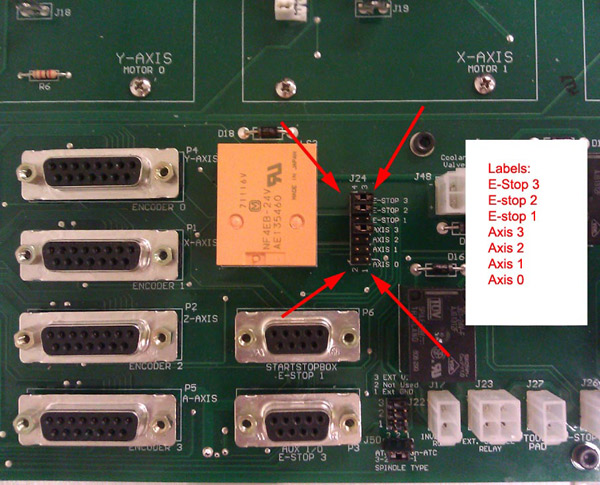 |
LC Control Board E Stop Jumper header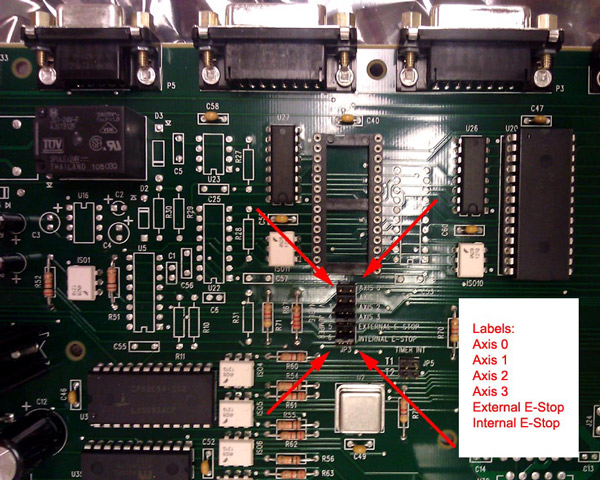 |
- Record which pins already have jumpers on them. This will be critical information later. Label this list "Original E-Stop Jumpers"
- Place jumpers on all of the headers.
- Power up and enable the machine. It should jog properly now.
- Power down the machine and remove ONE of the NEW e-stop jumpers
- Power up and enable the machine. If it jogs properly, power down and remove another NEW jumper.
- Once you have removed the jumper that causes the machine to no longer enable, you have found the cause of your problem.
If the jumper removed was for an axis, while the machine has its power locked out, closely inspect the rectangular cable that goes to the motor and the subsequent cable at the control board. Are any pins bent or shorter than others? Does the cable appear damaged along its length?
If the jumper removed was for an Emergency Stop, inspect the wiring inside the Emergency stop box. It is likely loose or broken.
After repairing the problem, be sure to restore the original state of the jumpers. You may be tempted to run the machine with all of the jumpers in place instead of fixing the cause of the problem. Note that this is a dangerous practice, as the machine cannot sense lost feedback and could result in an extremely high speed runaway axis.
If you are unable to locate the cause of the E-stop problem, contact tech support.
|
Estop noblink
Scenario: The ready light is not blinking while attempting to enable the controller. Controller box Your machine is using the LC Plus controller or a Premium Class controller. It is NOT a low power LC or LP controller. You receive one of the two following error boxes:
or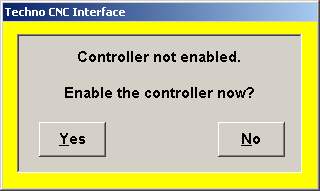 Problem: The machine is not connected to the PC, or the controller cable is damaged.
Solution:
- Power down the machine and computer and Lock out power.
- Ensure the cable that goes between the computer and the control box is secure on both ends. Verify control cable.
- Unlock power, power back up and test again.
If the ends are secure and the problem still occurs:
- If this is a new install or a new computer that has not yet worked properly, Verify the drivers for the system, as if they are not installed on an LC plus or Premium controller, this is a symptom.
- Power down the machine and computer and Lock out power.
- Disconnect the cable (from the PC first) and inspect the pins in the connector, then inspect the connector on the Control Board side. The PC Connector is more likely to have issues since it is more frequently removed and replaced by the user.
- Bent pins can be subtle and difficult to see. Inspect the cables very carefully. A pin does not need to be completely destroyed to cause a problem. Even slightly tilted pins can contact other pins when placed into the connector. If you are unsure about the integrity of the connector pins, carefully take a clear picture and email it to tech support.
|
Estop no ready light
Scenario: The machine is not enabling, and the controller is one which does not have a ready light indicator.
Controller_box Your machine is using the LC Plus controller or a Premium Class controller. It is NOT a low power LC or LP controller.
You receive one of the two following error boxes:
or Problem: The machine is not connected to the PC, or the controller cable is damaged.
Solution:
If there is not proper feedback:
- Power down the machine and computer and Lock out power.
- Ensure the cable that goes between the computer and the control box is secure on both ends. Verify control cable.
- Unlock power, power back up and test again.
If the ends are secure and the problem still occurs: - Power down the machine and computer and Lock out power.
- Disconnect the cable (from the PC first) and inspect the pins in the connector, then inspect the connector on the Control Board side. The PC Connector is more likely to have issues since it is more frequently removed and replaced by the user.
- Bent pins can be subtle and difficult to see. Inspect the cables very carefully. A pin does not need to be completely destroyed to cause a problem. Even slightly tilted pins can contact other pins when placed into the connector. If you are unsure about the integrity of the connector pins, carefully take a clear picture and email it to tech support.
|
Lock out power:
Locking out power:
Locking out power prevents the machine from harming the user while the machine is being worked on. Dangerous voltages and the potential for the machine to move will exist if the machine is powered up while it is being serviced.
NEVER WORK ON OR INSIDE A MACHINE THAT IS POWERED UP OR HAS THE POTENTIAL TO BE ACCIDENTALLY POWERED UP
The regulations at your workplace may vary from standard regulatory requirements. When conflicting regulations are encountered, follow your workplace regulations. If there is ANY uncertainty, contact your workplace supervisor.
Locking power out from a machine is required for any servicing. Power down the machine and the computer by the normal methods. Remove the power source from the machine and lock it out as per your workplace regulations. This may involve an actual lock on a breaker box, a nametag, or some similar methods.
Many machines have multiple sources of power (control box, spindle, etc). Be sure to find all power sources and lock all of them out prior to any service.
Position Error
Scenario:
You are repeatedly getting the following message box:
Problem:
The machine is unable to travel to the position that has been requested of it.
Solution: There are a few pieces of information necessary to determine the cause of this issue.
• Does the machine move properly in any of the axes?
If the machine does not move in any of the axes, you should Verify power to the machine
Run away:
Scenario
- When attempting to move an axis by jogging or when running a file, one axis "takes off",
usually resulting in a crash at the end of travel or a red box position error
- Ensure feedback in setup
- When axis is pushed by hand, the numbers in the Positional Display
for that axis do not reflect the change in position.
- When the Motor cable swap procedure is performed, the same axis exhibits this problem.
Problem: The encoder feedback data is not reaching the controller.
Solution:
- The most common cause is a damaged encoder. Contact tech support to discuss having the
encoder replaced.
-
Sometimes cables can be damaged and cause this problem. The potential cables for this
problem are the cable between the PC and the Controller box, and the rectangular cable
between the motor and the Controller box.
|
Verify Power:
To verify power to the machine, you must first ascertain which Controller box you are using.
LC / LP Controller box:
> Check the diagnostic LEDs on the front.
If PC is lit and no other LEDs are lit, the controller box is not receiving any external power. Verify the Power switch is on. Verify the power cable is plugged in and the outlet it is plugged into is live. Check the fuses in the Power receptacle.
If the PC, +5, +12, +24 lights are lit (ready is irrelevant in this scenario) and the +48 is not lit, the motor fuse inside the control box is blown. After performing Lock out power, replace the fuse with 5x20mm 10A 250v cartridge fuse.
LC Plus Controller box:
> Check the diagnostic LEDs on the front.
If the 24v LED is not lit, the controller box is not receiving any external power. Verify the Power switch is on. Verify the power cable is plugged in and the outlet it is plugged into is live. Check the fuses in the Power receptacle.
Servo Box 1,2:
> If the fan is not blowing in the back of the controller box, the controller box is not receiving any external power.
Verify the Power switch is on. Verify the power cable is plugged in and the outlet it is plugged into is live. Check the fuses in the Power receptacle.
|
Ensure feedback in setup:
To verify the system is communicating with the controller properly:
-
Depress the Emergency-Stop switch
- Start the CNC interface
- If there are warnings you are attempting to work around, dismiss them.
- Click Setup
- Click Diagnostics
- Push the machine in all possible axes and verify feedback on the axes in diagnostics as per the image below. For the Z axis, if it is not dangerous, depress the Brake switch momentarily, which will cause the axis to drop and provide feedback.
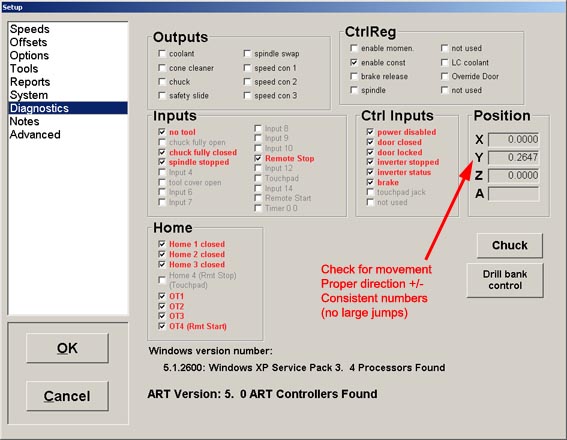
If all connected axes show proper and consistent feedback, then the connection is likely good.
If only some axes provide feedback:
The cable between the PC and the Controller box may be damaged
An encoder on the motor may be damaged
A motor signal cable may be damaged
A circuit board may be damaged. |
Controller box:
The controller box encloses the control electronics, and provides a safe environment. There are many ways to determine which controller your machine employs.
Note that this list is not exhaustive. Older and less common controllers are not listed here. If you do not see your controller here, obtain any part numbers or markings before contacting support.
*If possible, take a picture of the controller and email it to tech support.
Types Of Controllers |
LC Plus Controller

This is the current LC Plus control box. Note the Blue badge. This controller is frequently referred to as:
- High power controller
- LC plus, LC X or LC+ controller
- RG controller or New RG controller
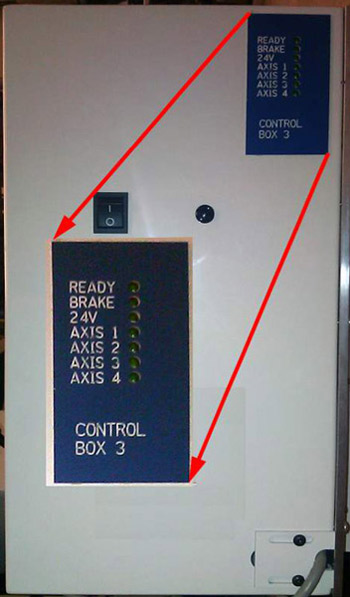 |
This is the current LC Plus control board inside the box
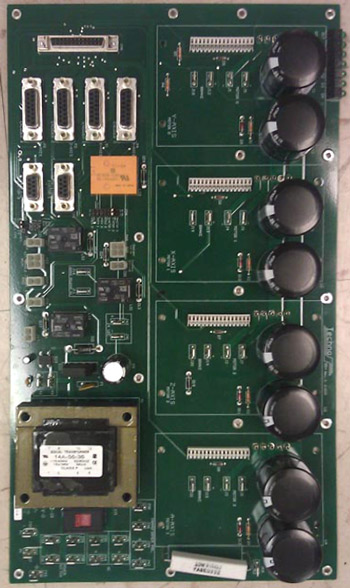
This is the PCI Card that will be inside the PC
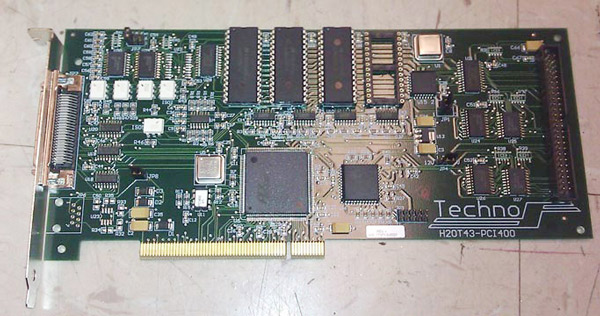 |
LC Control Box 
This is the current LC (AKA LP) control box. Note the Black badge. This controller is frequently referred to as:
- Low power controller
- LC or LC controller
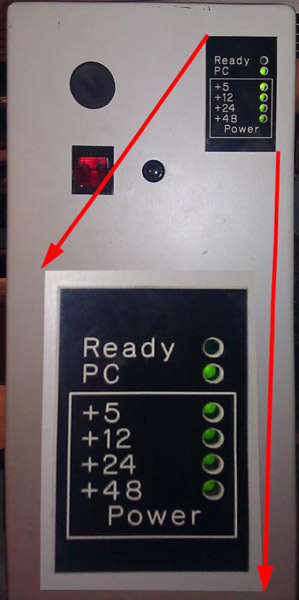
This is the current LC control board inside the box.
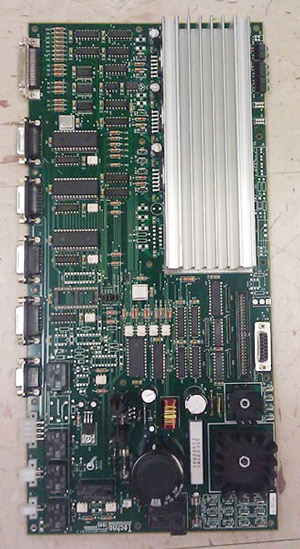
This is the PCI Card that will be inside the PC.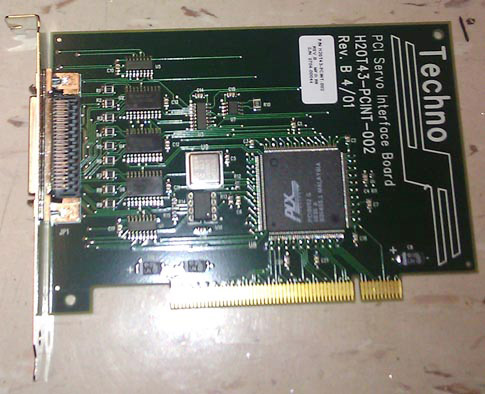 |
Servo Box 1 
This is the current MP Control Box This controller is frequently referred to as:
- Medium power controller
- Low Power RG controller
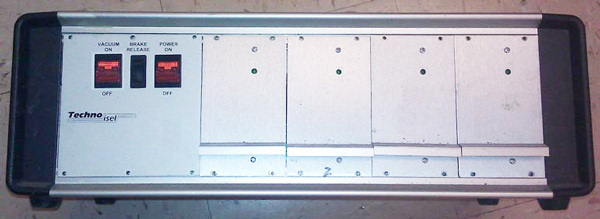
This is the PCI Card that will be inside the PC. NOTE: It is the same card as some other controllers.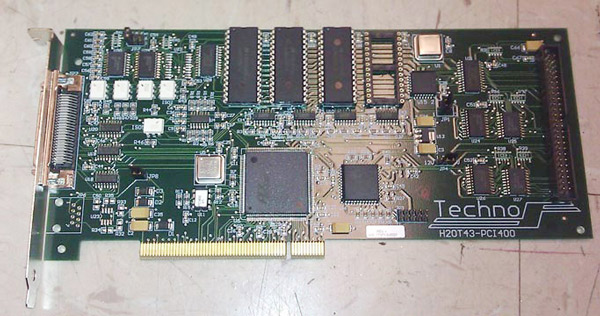
Servo Box 2
This is the current MP Control Box This controller is frequently referred to as:
- High power controller
- Old LC plus, LC X or LC+ controller
- Old RG controller
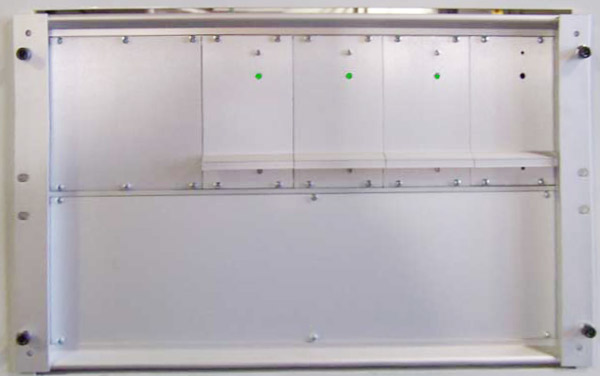
This is the PCI Card that will be inside the PC. NOTE: It is the same card as some other controllers.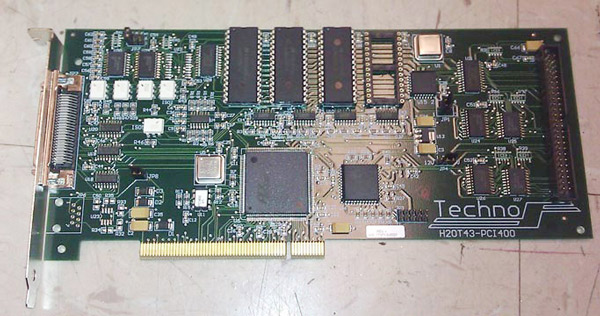
Premium Controller
This is the Premium Class console. This controller is frequently referred to as:
- High power controller
- Premium Class controller
- PC controller
This is the PCI Card that will be inside the PC. NOTE: It is the same card as some other controllers.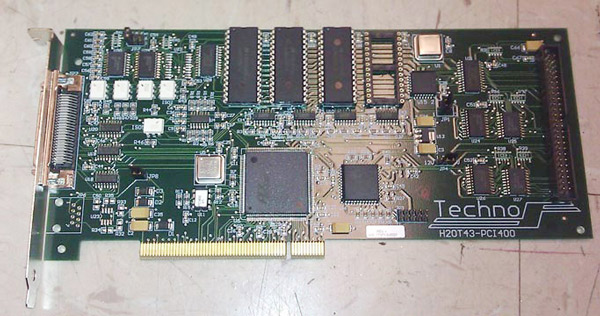
*You may also narrow down your controller type by the type of motor it is using. Note that this will not necessarily result in a perfect match.
- HP Motors go with LC Plus control boxes and Servo box 2 control boxes.
- LP Motors go with LC control boxes and Servo box 1 control boxes. The amperage is different between * LP size motors, please note it (listed on the motor sticker) before contacting tech support.
For reference, note the ratio of the size of the encoder housing (aluminum tube with the cables in the back) to the motor body.
- If the body is larger, it is a high power, LC+, RG style motor.
- If the housing is bigger, it is a low or medium(rare) power motor.
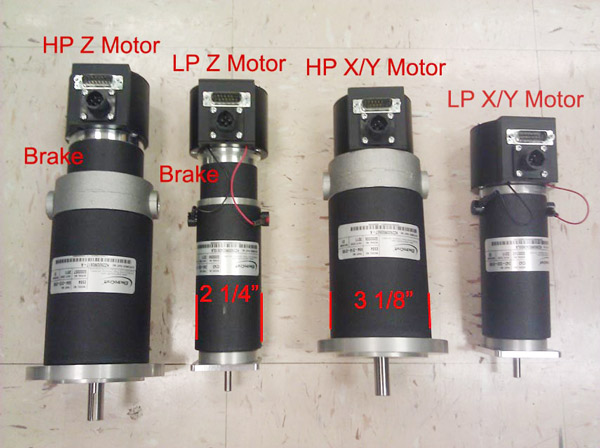 |
Power receptacle:
The power receptacle is located at the back of the box.
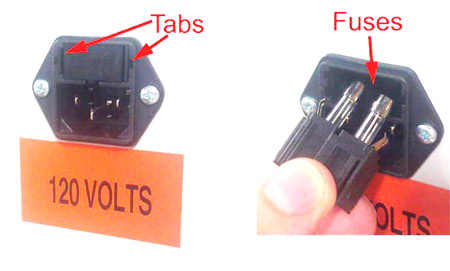 It will have the power cable running into it.
To check the fuses:
- Lock out power
-
On receptacles made after 2007, there are two tabs on the side. Press them inwards to extract the fuse holder.
-
On some older units, you may need to use a small screwdriver at the bottom of the fuse holder to pop it out.
-
Use a Multimeter to verify the fuses. Sometimes fuses that look good are burned.
Multimeter: This is a picture of a multimeter.
Yours may look different, but the important symbols should be the same.
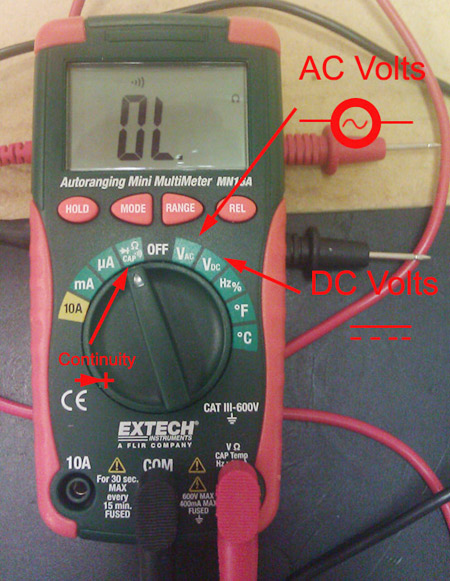 |
Set the origin Setting the origin
For proper operation, the machine has to "match" up the coordinate system with that of the drawing that it is running.
The origins are sometimes referred to the zeroes. Do not confuse this position with the home, which is a the end of travel of all of the axes.
The origin of the material is typically at one of the corners of the part. Sometimes it is in the middle of the part. Common to cabinet making and some other woodworking applications where stock isn't flat and veneers are involved, the Z zero is at the bottom of the material.
The origin of the part in the CAM software relative to the material must match the origin of the machine relative to the material in the real world. If these origins do not match, the part will not be cut properly.
To set an origin, jog the machine to where the origin is and click Zero on the interface and then All.
To quickly set the origin for the Z axis only, use the touchpad by placing the touchpad on the surface that is to be Z zero, hovering above the pad, and clicking Tool, then Touch off Z zero. Note that this will not set the X and Y zero.
To adjust the origins by a set amount without moving, double-click the origin readout in the upper right of the interface and enter values by which to move the origin around. This is especially useful for moving the origin to a spot that is not physically achievable.
|
Frozen axis A frozen axis is one that will not move by way of the controller, and cannot be manually moved by the user when the machine is powered down.
Scenario:
- Axis will not move via interface and cannot be moved manually.
- Receives "M-x Position error, no power to controller. Re-enable controller?", error
- Can jog other axes
- Customer is probably cutting wood or another material where a lot of debris is generated.
Problem: The ball nut is possibly jammed-up with debris. This is especially likely if the machine is used to cut wood or other material that easily becomes airborne after being cut.
Solution:
- Obtain a can of WD-40 that still has the red straw.
- Hit "E-Stop" and POWER DOWN machine Lock out power
- Thread the red straw from WD-40 can into groove of ball screw and into the ball nut and blow it out with copious amounts of WD-40. This will be messy, avoid being underneath the nut during this process. Take all necessary precautions to prevent eye and lung exposure to oils.
- After putting a lot of WD-40 into the ball nut, attempt to spin it by hand, being careful around the belt and pulley. This will force the debris out of the nut.
- Once the machine is moving again remove all the WD-40 with a rag and lubricate the machine. DO NOT leave the WD-40 residue on the ball screw. Also note that over lubricating the machine in a dusty environment frequently leads to this problem, as the dust gets stuck to the excessive debris.
|
Amplifier status
It may be necessary to check to see if an amplifier is enabling.
First, find your Controller box.
On the LC Plus control box:
-
The amplifier status is read out on the badge in the front. Axis 1,2,3,4 have lights. If the light is lit, the amplifier is enabled.
- If no lights are lit, the problem is likely the transformer. Find a qualified electrician with a multimeter and then Contact Support.
- If some lights are lit and others are not, the problem is likely the amplifiers. The box will need servicing. Contact Support.
On Premium Class control box:
-
The amplifiers are blue boxes inside the console.
- Access to the console should only be attempted by a qualified electrician. The control box has multiple high voltage sources.
- Once access is granted, there will be 3 or 4 blue boxes with green or red blinking LEDs.
- If the LEDS are not lit, there is no power.
- If the LEDS are red, there is an error.
- If the LEDS are solid green, that amplifier is enabled and working properly
- If the LEDS are blinking green, that amplifier is disabled but working properly.
On the Servo Box 1 and 2:
- The LEDS across the front of the box (horizontally) represent the amplifier status.
- Unlit means the amps are not enabled.
- Lit means the amplifiers are enabled.
- If some amps are lit and others are not, there is likely a problem with the amplifier.
Amplifier status is not observable on the low power LC control box. |
Axis tightness
In rare circumstances, one of the axes may suffer from tightness in only certain spots.
To find this tightness, there is an axis lag test that can be run. This test is available in 1.421.10 and higher.-
Move the machine to an inch or so before the problem spot.
- Click Help
- Click Machine test, then read and understand the warning.
- You will be presented with the machine test screen, as follows:(Your version may have the buttons named "Run--v", but the function is the same.)
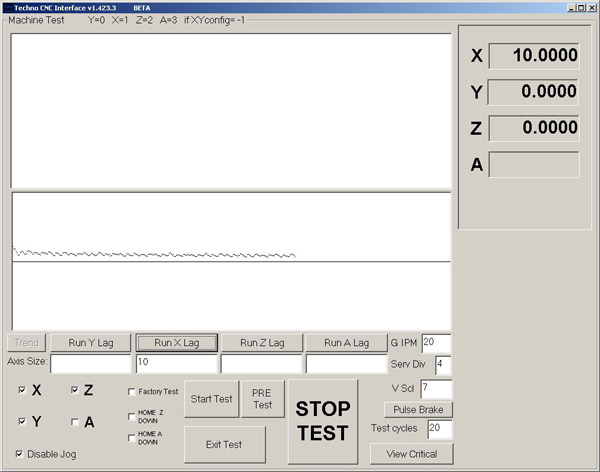
- Enter a distance (negative or positive) in the text box below the axis you wish to test.
- Set the G IPM to a low number, like 20. This is the speed at which it will test.
- Click the Run [xyza] lag button (or the run--v button)
- The axis will creep along slowly, showing the servo lag.
The results may be difficult to interpret. When in doubt, shift-click the image to save a screen capture of it to c:\mechanics.jpg and email techno the file. You are looking not for high amounts of lag, but lag that increases or decreases in magnitude (spikes or slants).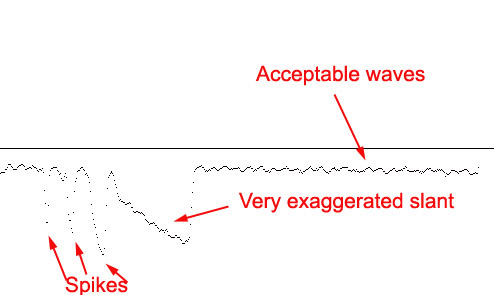 |
|